![]() | |
Names | |
---|---|
IUPAC name
Bis(prop-2-enyl) carbonate | |
Identifiers | |
| |
3D model (JSmol) |
|
EC Number |
|
PubChem CID |
|
UNII | |
CompTox Dashboard (EPA) |
|
| |
| |
Properties | |
C7H10O3 | |
Molar mass | 142.154 g·mol−1 |
Density | 0.991 g/mL |
Melting point | −70 °C (−94 °F; 203 K) |
Boiling point | 95–97 °C (203–207 °F; 368–370 K) 60 mmHg |
Except where otherwise noted, data are given for materials in their standard state (at 25 °C [77 °F], 100 kPa).
Infobox references |
Diallyl carbonate (DAC) is a colorless liquid with a pungent odor. Its structure contains allyl groups and a functional carbonate group.[1] The presence of double bonds in the allyl groups makes it reactive in various chemical processes. This compound plays a key role in the production of polymers, including polycarbonates and polyurethanes. Diallyl carbonate is soluble in ethanol, methanol, toluene, and chloroform. Diallyl carbonate reacts with amines, alcohols, and thiols.
DAC is also used as an acrylate agent. Allyl carbonates are widely used in Tsuji-Trost allylation, promoting the formation of carbanions, boronates, phosphides, amides, and alkoxides. They act as in situ nucleophiles, increasing the reaction rate compared to allyl acetate. These compounds are of great interest for the design of intramolecular decarboxylate asymmetric compounds.
History
The Tsuji-Trost reaction was first introduced in 1962. This method played an important role in the synthesis of diallyl carbonate. The first mention of its commercial production dates back to 1982, when Tokuyama Corporation synthesized it for the first time using the sodium carbonate method.[2] This milestone marked the beginning of the sale of diallyl carbonate as a raw material for the production of plastic lenses.
Synthesis
Method 1
DAC can be synthesized by the reaction of alcohol with the highly toxic gas phosgene. The second chlorine atom in phosgene increases the electrophilicity of the carbonyl carbon atom. As with the reaction of alcohols with acid chlorides, a base is required to neutralize the byproduct, hydrogen chloride (HCl), so that it does not interfere with the synthesis and ensures the overall efficiency of the process. In this process, the alcohol undergoes acylation, in which the hydroxyl group of the alcohol reacts with phosgene to form the intermediate acyl chloride. This intermediate can further react with another alcohol molecule or other nucleophiles to give the desired diallyl carbonate (DAC).[3]

Method 2
The synthesis of diallyl carbonate (DAC) usually takes place in a two-stage process that begins with the reaction between urea and allyl alcohol. In the first stage, this reaction proceeds rapidly and yields acetaldehyde as an intermediate product. However, to achieve the final production of DAC, a more complicated second stage is required, which is only possible in the presence of a catalyst.[4]
The second step is the conversion of acetaldehyde to diallyl carbonate, a critical step in DAC synthesis. The catalyst plays a crucial role as it facilitates the reaction and increases the efficiency of the conversion of acetaldehyde into the desired diallyl carbonate. In this particular process, LaCl3 serves as the catalyst.
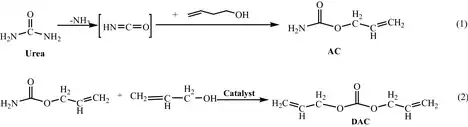
Method 3
The base, in this case pyridine, is used to neutralize the hydrogen chloride (HCl) produced in the reaction. The reaction mechanism involves a nucleophilic substitution of the chlorine atom in the allyl chloroformate by the hydroxyl group in the allyl alcohol, which leads to the formation of diallyl carbonate.[5]
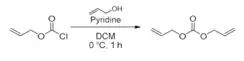
Method 4
This method enables not only the production of diallyl carbonate, but also of diethyl carbonate, dibutyl carbonate and bis((2,2-dimethyl-1,3-dioxolan-4-yl)methyl)carbonate. Catechol carbonate (CC) is synthesized by the carbonate exchange reaction (CIR) between dimethyl carbonate (DMC) and catechol using a sodium methoxide catalyst. After the production of catechol carbonate, the next step in the production process is a reaction between catechol carbonate and allyl alcohol in reactive distillation system (RDS). Sodium methoxide serves as a catalyst in this step[6]

Polymers
poly (OESDAC-co-ADC)
This polymer comprises 2,2'-(oxybis(ethylene sulfonyl)) diallyl carbonate (OESDAC) and its copolymers with allyl diglycol carbonate (ADC), wherein the resulting polymer can be further converted into a film. OESDAC was synthesized in two steps. First, a condensation of 2,2'-bis(2-hydroxyethylsulfanyl)diethyl ether with 3,9-dithia-6-oxa-undecane-1,11-diol-bis(allyl carbonate) was carried out in the presence of alkali at low temperatures. Second, the oxidation of 3,9-dithia-6-oxa-undecane-1,11-diol bis(allyl carbonate) with hydrogen peroxide in acidic medium was carried out. The synthesis of ADC involved the condensation of diethylene glycol with allyl chloroformate in the presence of pyridine at low temperatures.
The copolymerization of OESDAC and ADC was performed in the presence of the initiator IPP and the plasticizer DOP. The resulting polymer films can be used as nuclear trace detectors to record and study traces of energetic particles such as alpha particles and fission fragments.[7].
poly(1-benzoate-2,3-diallylcarbonate glycerol
The polymer poly(1-benzoate-2,3-diallylcarbonate glycerol) was obtained from the monomer BDACG, which underwent gamma irradiation in a vacuum at various doses and temperatures using a 60°C gamma irradiation source. This process resulted in the formation of branched polymers (PBDACG) with different gel contents.
Additionally, BDACG was subjected to UV irradiation in the presence of the photoinitiator Darocur 1173, leading to the formation of a polymer with high gel content and a network structure.
The results and conclusions indicate that gamma-polymerized BDACG forms thermoplastic polycarbonates with crosslinking ability in the solid state. Conversely, photopolymerized BDACG forms polymers with high gel content suitable for applications in optics and as nuclear track detectors.
Applications include the use of gamma-polymerized BDACG for producing transparent thermoplastic polycarbonates in optical applications and as materials with internal crosslinking. Photopolymerized BDACG is suitable for polymers with high gel content, making them applicable in optical purposes and as nuclear track detectors in technical areas[8].
Polycarbonate
The monomer (1,1'-biphenyl)-4,4'-diallylcarbonate was synthesized by reacting 4,4'-biphenyl, pyridine, and allyl chlorocarbonate at 5°C. Simultaneously, the monomer hexa(4-allylcarbonatephenoxy)cyclotriphosphazene was prepared by the reaction of Allyl(4-hydroxyphenyl) carbonate with hexachlorocyclotriphosphazene.
Following the acquisition of the two monomers, a polymerization process was conducted by reacting them together, utilizing benzoyl peroxide as the initiator. Two distinct polycarbonates were produced: the first after three hours of polymerization and the second after 34 hours. The primary distinction lies in their thermal stability, with the first polycarbonate remaining stable up to 250 °C, while the second begins decomposition at 240 °C. At 800 °C, the first polycarbonate loses 90% of its mass, whereas the second polycarbonate only loses 28%. Additionally, the second polycarbonate exhibits a higher limiting oxygen index (LOI) of 46.3%. In comparison to the classic polycarbonate, the second polycarbonate demonstrates a superior LOI but has lower thermal stability, remaining stable only up to 150 °C[9].
Non-isocyanate polyurethane
Diallyl carbonate was used to synthesize the polymer by thiol-ene reaction with dithiols. This component was synthesized from hydroxamic acid and diallyl alcohol with the participation of TBD catalyst. The result was a carbonaceous polymer with high viscosity and transparency. The polymer has thermal properties such as glass transition at temperatures between -12 and -15 °С, and a reduction in crystallization was observed due to the introduction of bulk groups[10].
The synthesis of non-isocyanate polyurethanes involves the reaction of hydroxamic acid with two equivalents of diallyl alcohol and catalytic amounts of TBD as a base in diallyl carbonate. The reaction mixture is heated at 110 °C overnight using a methodology described for catalytic Lossen rearrangements. This process results in the formation of both carbamate and urea. Subsequently, a reaction takes place between cyclooctane-1,4-diol and either carbamate or urea. The obtained compounds are then polymerized via a highly efficient thiol–ene reaction, leading to the production of non-isocyanate polyurethanes with Mn values up to 26 kg/mol, containing thioether linkages.
Similarly, the primary by-product of the Lossen rearrangement, symmetric urea, can be polymerized using the same method. Importantly, from an ecological perspective, the monomeric mixture can be directly utilized without the need for separation.[10]
Lignin
Diallyl carbonate can be utilized for the alkylation of beech wood organosolv lignin (OL). The process involves the reaction between diallyl carbonate and the hydroxyl groups of lignin, with tetrabutylammonium bromide (TBAB) serving as a catalyst. This resulted in the formation of allyl functional groups within the lignin structure. The thermal properties of the allylated lignin decrease with an increase in the degree of alkylation. Additionally, the allylated lignin exhibits lower thermal stability compared to the unmodified lignin, possibly due to the high reactivity of the allyl functional groups. The obtained allylated lignin can be employed for further reactions, such as olefin metathesis[11].
Application
The use of diallyl carbonate is widespread in the industry due to its unique properties. It plays a crucial role in polymer production, serving as a key component in the creation of various polymers. Diallyl carbonate is utilized to produce high-performance polymers, such as those found in polycarbonates and polyurethanes. These polymers find diverse applications, including the production of optical plastics, engineering plastics, and other specialty materials.
In Tsuji-Trost allylation reactions, a widely used organic synthesis method, Diallyl carbonates play a significant role. They function as acylating agents, facilitating the introduction of allyl groups into various organic compounds. This results in the formation of carbanions, boronates, phosphides, amides, and alkoxides.
Diallyl carbonate also serves as a solvent in various chemical reactions. Additionally, its antibacterial properties make it applicable in various medical fields. Moreover, its potential applications in solvents, agrochemicals, and pharmaceutical industries have been widely demonstrated.[4]
The transesterification process involving Diallyl carbonate and glycerol, catalyzed by Pd/PPh3, produces glycerol carbonate.[12] Glycerol carbonate finds application in coatings, paintings, and adhesive industries, further highlighting the versatility of Diallyl carbonate in various industrial processes.
References
- ↑ "Buy Diallyl carbonate | 15022-08-9". Smolecule. Retrieved 2023-11-26.
- ↑ "Tokuyama". www.tokuyama.co.jp. Retrieved 2023-11-26.
- ↑ "ジアリルカーボネート". プラスチック素材辞典 (in Japanese). 2022-10-27. Retrieved 2023-11-26.
- 1 2 Wang, Dengfeng; Zhang, Xuelan; Luo, Hainan; Wei, Shuwei; Zhao, Xueying (2019-04-15). "Direct Synthesis of Diallyl Carbonate Via Urea Transesterification with Allyl Alcohol Over Metal Chlorides". Catalysis Letters. 149 (4): 1067–1074. doi:10.1007/s10562-019-02693-y. ISSN 1011-372X.
- ↑ Etkind, Samuel I. (2017). "The Synthesis of Novel Cyclohexyne Precursors for an Intramolecular Pauson-Khand Type Reaction". Texas journal. University of Texas at Austin. doi:10.15781/T2TB0Z13F.
- ↑ Tabanelli, T.; Monti, E.; Cavani, F.; Selva, M. (2017-03-20). "The design of efficient carbonate interchange reactions with catechol carbonate". Green Chemistry. 19 (6): 1519–1528. doi:10.1039/C6GC03466G. ISSN 1463-9270.
- ↑ Shetgaonkar, Abhijit D.; Mandrekar, Vinod K.; Nadkarni, Vishnu S.; Naik, Diptesh G. (2023-11-01). "Novel poly (disulfonyl diallyl carbonate) polymers for swift solid state nuclear track detection applications". Radiation Measurements. 168: 107002. doi:10.1016/j.radmeas.2023.107002. ISSN 1350-4487.
- ↑ López, Delia; Plata, Pedro; Burillo, Guillermina; Medina, Carlos (August 1997). "Synthesis and radiation polymerization of 1-benzoate-2,3-diallylcarbonate glycerol". Radiation Physics and Chemistry. 50 (2): 171–173. doi:10.1016/s0969-806x(96)00187-9. ISSN 0969-806X.
- ↑ Herrera-González, A M; García-Serrano, J; Pelaez-Cid, A A; Montalvo-Sierra, I (2013-06-07). "Efficient method for polymerization of diallycarbonate and hexa(allylcarbonate) monomers and their thermal properties". IOP Conference Series: Materials Science and Engineering. 45: 012008. doi:10.1088/1757-899x/45/1/012008. ISSN 1757-8981.
- 1 2 Filippi, Luca; Meier, Michael A. R. (February 2021). "Fully Renewable Non‐Isocyanate Polyurethanes via the Lossen Rearrangement". Macromolecular Rapid Communications. 42 (3). doi:10.1002/marc.202000440. ISSN 1022-1336.
- ↑ Over, Lena C.; Meier, Michael A. R. (2015-12-21). "Sustainable allylation of organosolv lignin with diallyl carbonate and detailed structural characterization of modified lignin". Green Chemistry. 18 (1): 197–207. doi:10.1039/C5GC01882J. ISSN 1463-9270.
- ↑ "Diallyl Carbonate | 15022-08-9". ChemicalBook. Retrieved 2023-11-26.